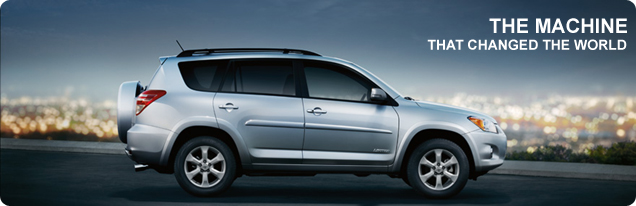
Characteristics
• This layout that uses standardized processing operations to achieve smooth, rapid, high-volume flow
• It is made possible by highly standardized goods or services that allow highly standardized, repetitive processing
• The work is divided into a series of standardized tasks, permitting specialization of equipment and division of labor
• Product layouts arrange this standardized tasks in a line according to the sequence of operations that need to be performed to assemble a particular product
• Each Product should have its own "line"
• Product layouts are suitable for mass production or repetitive operations in which demand is steady and volume is high because of this product layouts are more autonomous than process layouts
• The major concern in a product layout is balancing the assembly line so that no one workstation becomes a bottleneck and holds up the flow of work through the line
• A product layout needs material moved in one direction along the assembly line and always in the same pattern
• The most common material handling equipment used in product layouts is the conveyor; conveyors can be automatic (at a steady speed), or paced by the workers
• Aisles are narrow because material is moved only one way, it is not moved very far
• Scheduling of the conveyors, once they are installed, is simple--the only variable is how fast they should operate
• Storage space along an assembly line is quite small because in-process inventory is consumed in the assembly of the product as it moves down the assembly line
• Finished good inventory may require a separate warehouse for storage before they are sold
• The large volumes handled by these systems usually make it economical to invest substantial sums of money in equipment and in job design.
Advantages of Product Layout
• Faster processing rates (High volume)
• Lower inventories
• Less unproductive time lost to changeovers and materials handling
• Low unit cost
• Low labor skill needed
• Low material handling cost
• High utilization of labor and equipment
• Simple routing and scheduling
• Routine accounting, purchasing and inventory control
• High efficiency and utilization
• Simple to track and control
Disadvantages of Product Layout
• Lacks flexibility to changes in Volume, design, mix
• Highly susceptible to shutdowns: Can not accommodate partial shut downs/breakdowns
• Boring for labor: Creates dull, repetitive jobs
• Poorly skilled workers may not maintain equipment or quality of output
• Needs preventive maintenance
• Low motivation
1. Low worker enrichment
2. Individual incentive plans are not possible
Product Layouts Designing Considerations
• Line balancing
attempt to equalize the amount of work at each work station and cuts down on idle time for the workers
• Pacing
The movement of product from one station to the next as soon as the cycle time has elapsed.
• Behavioral factors of workers
• Number of models produced
A mixed-model line produces several items belonging to the same family.
• Cycle times
depend on the desired output rate, and efficiency varies considerably with the cycle time selected.
Line Balancing
• In Line Balancing Tasks are grouped into manageable bundles and assigned to workstations with one or two operators
Goals
• to have approximately equal time requirements for each workstations
• to achieve the desired output rate with the smallest number of workstations
• to minimize idle time along the line, which leads to high utilization of labor and equipment
Causes for Imperfect Balancing
Perfect balance is often impossible to achieve because:
• Some task groupings are undesirable
Require different skills
Incompatible materials
Equipment that can't fit at the same station
• Differences among elemental task lengths may not be overcome by grouping tasks
• Required technological sequence may prohibit desirable task combinations
Line Balancing Design Considerations
When designing a product layout line balancing two constraints be considered
• Cycle time
It refers to the maximum amount of time the product is allowed to spend at each work station if the schedule production rate is to be reached
• Precedence requirements
They are physical restrictions on the order in which operations are performed on the assembly line
a. Cycle Time
• Cycle time, refers to the maximum amount of time the product is allowed to spend at each workstation if the targeted production rate is to be reached.
• Desired cycle time is calculated by dividing the time available for production by the number of units scheduled to be produced:

• Suppose a company wanted to produce 120 units in an eight-hour day. The cycle time necessary to achieve that production quota, is
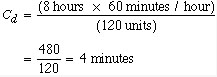
Cycle Time & Flow Time
• Cycle time can also be viewed as the time between completed items rolling off the assembly line.
• Consider the three-station assembly line shown here.
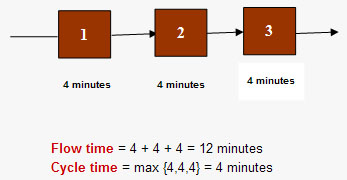
• It takes 12 minutes (i.e., 4 + 4 + 4) for each item to pass completely through all three stations of the assembly line.
• The time required to complete an item is referred to as its Flow time, or Lead time.
• However, the assembly line does not work on only one item at a time.
• When fully operational, the line will be processing three items at a time, one at each workstation, in various stages of assembly.
• Every 4 minutes
a new item enters the line at workstation 1,
an item is passed from workstation 1 to workstation 2,
another item is passed from workstation 2 to workstation 3, and
a completed item leaves the assembly line.
• Thus, a completed item rolls off the assembly line every 4 minutes.
• This 4-minute interval is the actual cycle time of the line.
Actual Cycle Time
• The actual cycle time, Ca, is the maximum workstation time on the line.
• It differs from the desired cycle time when the production quota does not match the maximum output attainable by the system.
• Sometimes the production quota cannot be achieved because the time required for one work element is too large.
• To correct the situation, the quota can be revised downward or parallel stations can be set up for the bottleneck element.
Line Efficiency and minimum number of workstations
• Line balancing is basically a trial and error process.
• We group elements into work stations recognizing time and precedence constraints.
• For simple problems, we can evaluate all feasible groupings of elements.
• For more complicated problems, we need to know when to stop trying different workstation configurations.
• The efficiency of the line, E, and minimum number of workstations, N, can provide us guidelines
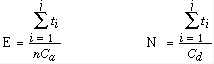
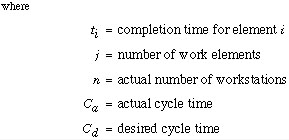
• The total idle time of the line, called balance delay, is calculated as (efficiency).
• Efficiency and balance delay are usually expressed as percentages.
• In practice, it may be difficult to attain the theoretical number of workstations or 100 percent efficiency.
Example 1: Cycle Times
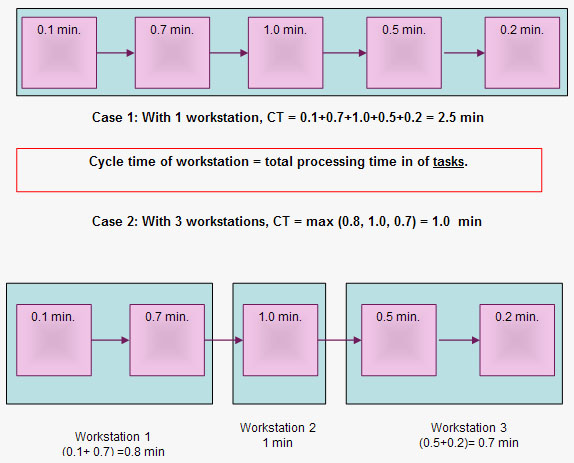
For 8 working hours per day
Operation Time OT = 8 x 60 = 480 minutes per day
• Case 1: Cycle Time CT = 2.5 min
Output = OT/CT = 480/2.5 = 192 units per day
• Case 2: Cycle Time CT = 1.0 min
Output = OT/CT = 480/1.0 = 480 units per day
b. Precedence Diagram
• The precedence diagram is a network, with work elements represented by circles or nodes and precedence relationships represented by directed line segments connecting the nodes.
• Immediate predecessors are work elements that must be done before the next element can begin.
• Precedence diagram allows one to visualize immediate predecessors better; work elements are denoted by circles, with the time required to perform the work shown below each circle.
• Precedence diagram is a tool used in line balancing to display elemental tasks and sequence requirements.
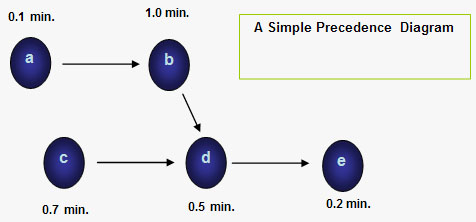
Line Balancing Rules
Some Heuristic (intuitive) Rules
• Assign tasks in order of most following tasks
Count the number of tasks that follow
• Assign tasks in order of greatest positional weight.
Positional weight is the sum of each taskĄ¯s time and the times of all following tasks.
Example 2: Assembly Line Balancing
Using the Figure above do each of the following:
1. Assuming an eight-hour workday, compute the cycle time needed to obtain an output of 480 units per day.

2. Determine the minimum number of workstations required.
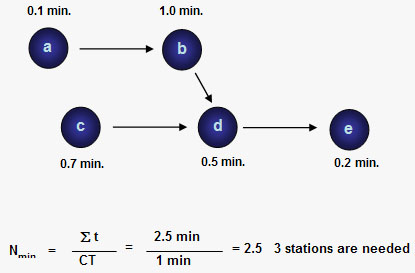
3. Assign tasks to workstations using the greatest positional weight
Positional weight for (a) = 0.1 + 1.0 + 0.5 + 0.2 = 1.8 min.
Positional weight for (b) = 1.0 + 0.5 + 0.2 = 1.7 min.
Positional weight for (c) = 0.7 + 0.5 + 0.2 = 1.4 min.
Positional weight for (d) = 0.5 + 0.2 = 0.7 min.
Positional weight for (e) = 0.2 min.
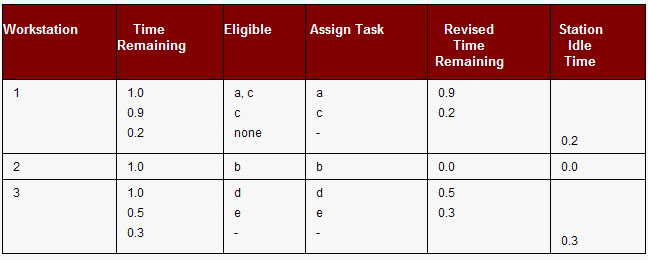
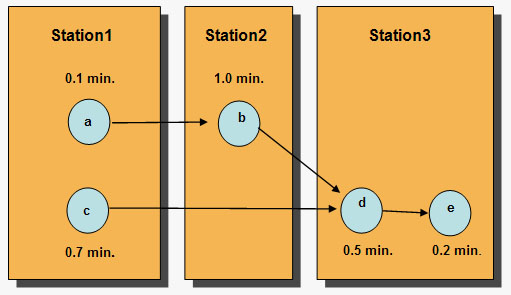
4. Measure Line balance effectiveness
Two widely used measures of effectiveness
• Balance Delay: The percentage of idle time of the line.

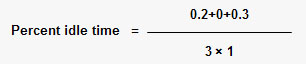
• Efficiency
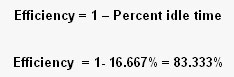
c. Line Balancing Procedure
1. Determine the cycle time and the minimum number of workstations.
2. Make assignments to workstations in order, beginning with Station #1. Tasks are assigned to workstations moving from left to right through the precedence diagram.
3. Before each assignment, use the following criteria to determine which tasks are eligible to be assigned to a workstation:
All preceding tasks in the sequence have been assigned.
The task time does not exceed the time remaining at the workstation.
If no tasks are eligible, move on to the next workstation
4. After each task assignment, determine the time remaining at the current workstation by subtracting the sum of times for tasks already assigned to it from the cycle time
5. Break ties that occur using one of these rules:
Assign the task with the longest task time.
Assign the task with greatest number of followings.
6. If there is still a tie, choose one task arbitrarily.
7. Continue until all tasks have been assigned to workstations.
8. Compute appropriate measures (e.g., percent idle time, efficiency) for the set of assignments.
Example 3: Assembly Line Balancing
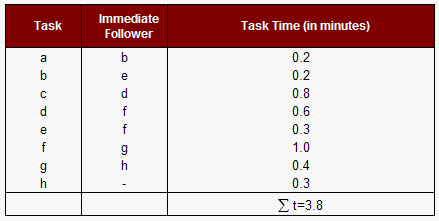
Solution to Example 3
1. Draw a precedence diagram
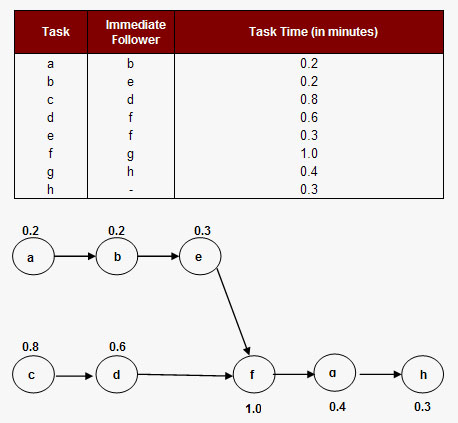
2. Assuming an eight-hour workday, compute the cycle time needed to obtain an output of 400 units per day.

3. Determine the minimum number of workstations required.

4. Assign tasks to workstations using this rule: Assign tasks according to greatest number of following tasks. In case of a tie, use the tiebreaker of assigning the task with the longest processing first.
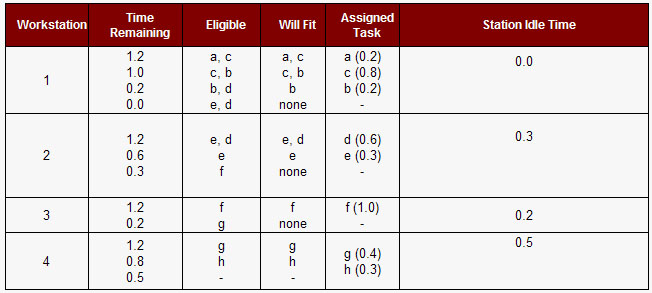
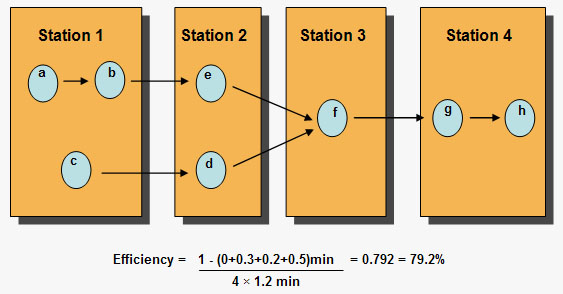
Example 4: Parallel Workstations
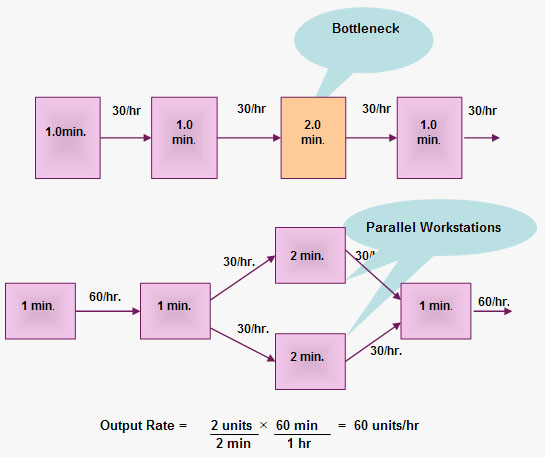
Two widely used measures of effectiveness
• Balance Delay

• Efficiency

d. Computerized Line Balancing
• Because complicated calculations are involved in line balancing software packages have been developed to assist this process
• IBM's COMSOAL (Computer Method for Sequencing Operations for Assembly Lines) and GE's ASYBL (Assembly Line Configuration Program) are 2 popular packages
» More Information